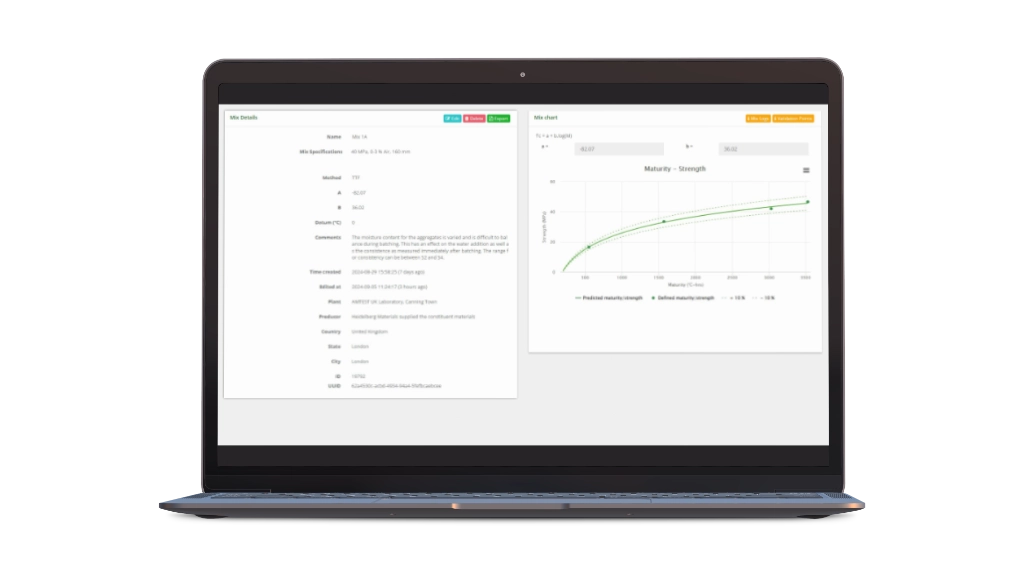
Research and Development
Our dedicated research and development lab ensures we can always come up with the optimised concrete mix design for your project.
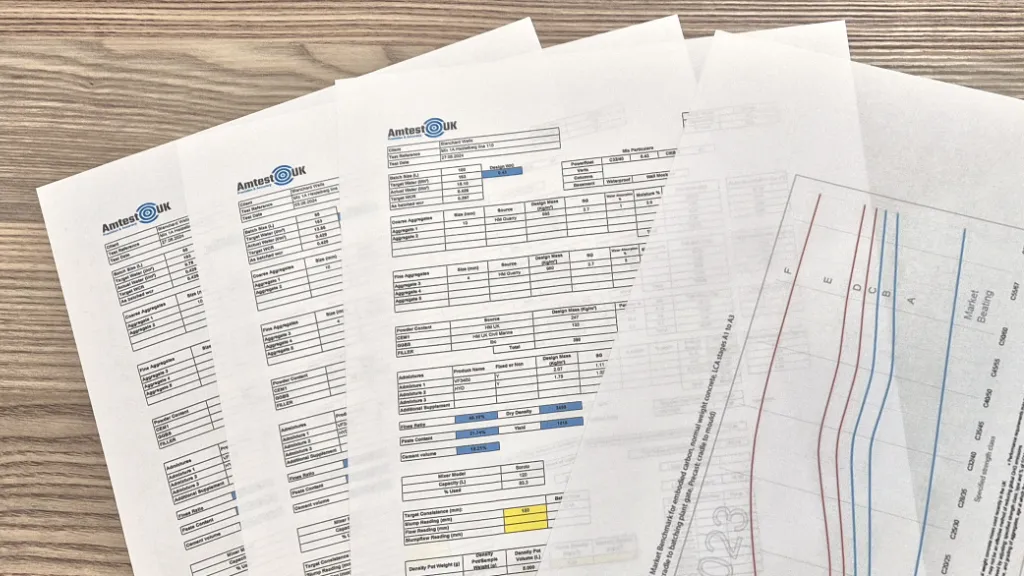
Step 1: Design
The process begins with creating a custom concrete mix design. We analyse the project requirements and design a mix that balances strength, durability, and workability. This step ensures that the final product meets performance criteria for any application.
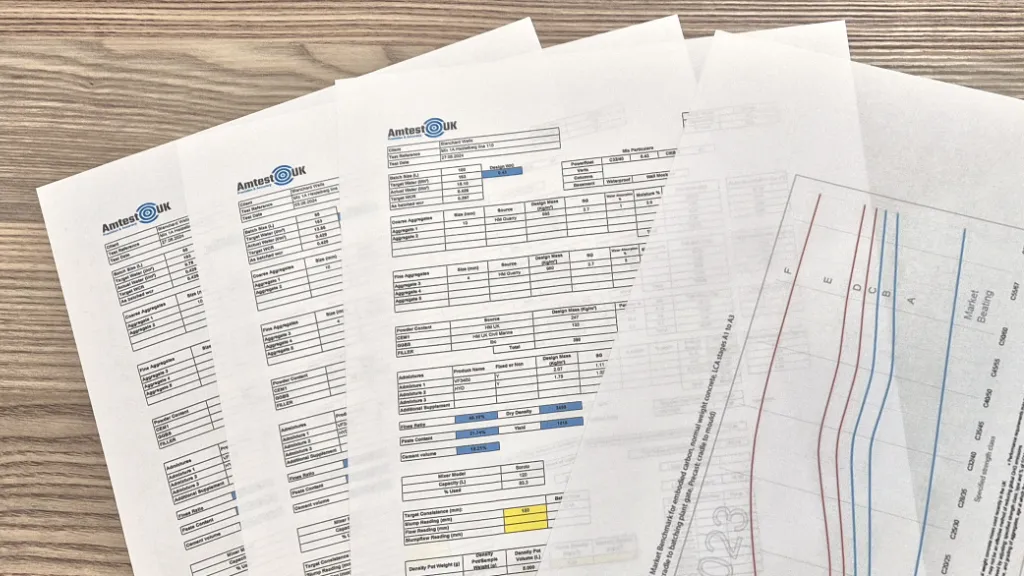
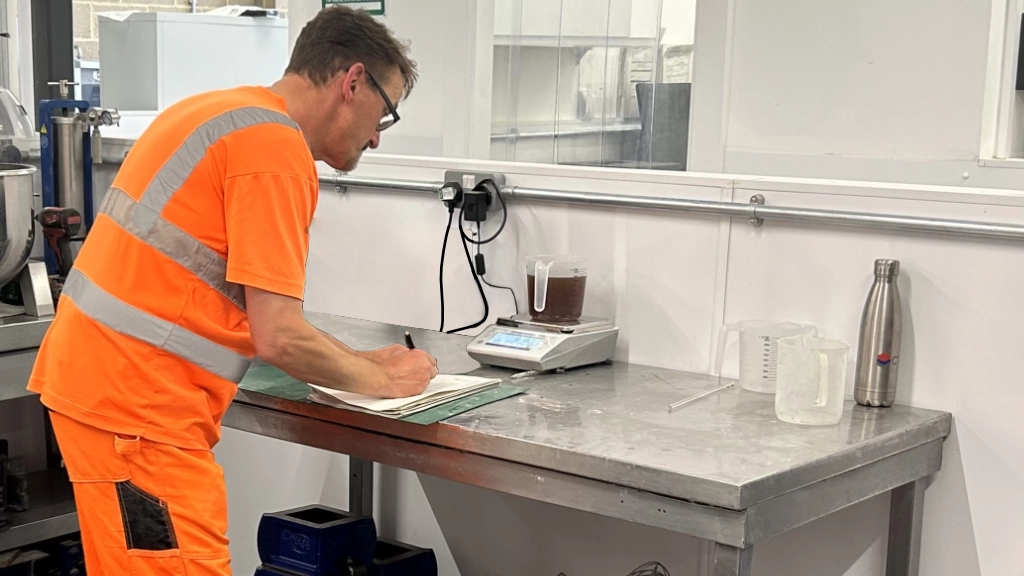
Step 2: Weighing
Accurate measurement of materials is critical. We carefully weigh all components, including cement, aggregates, water, and additives, to maintain consistency and control over the mix’s properties.
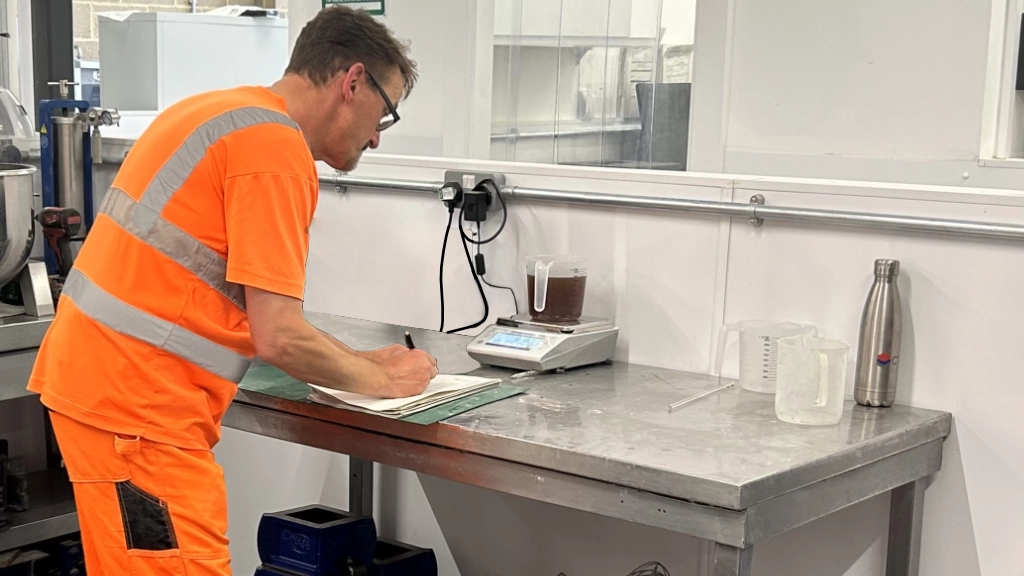
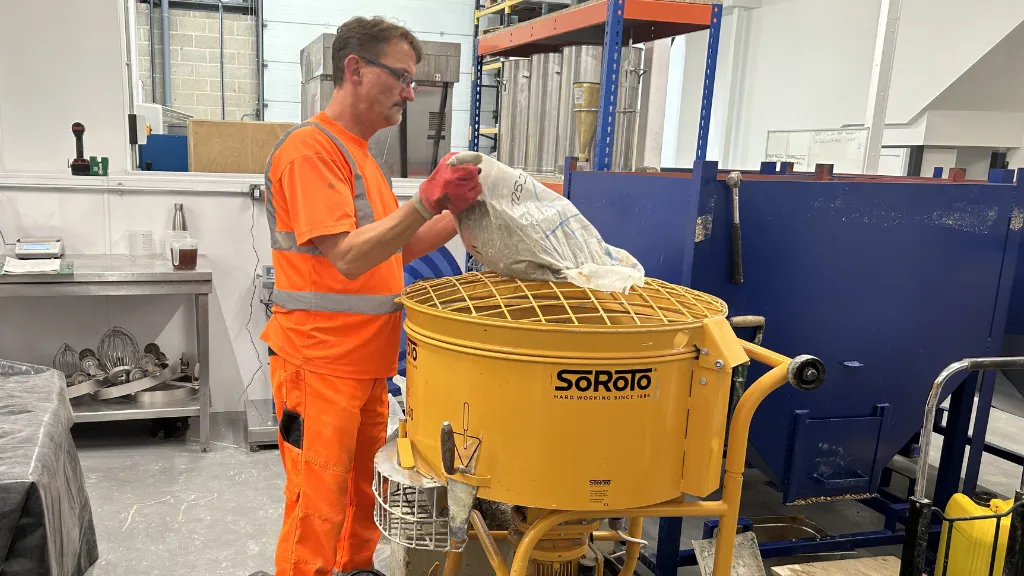
Step 3: Batching
Once the components are weighed, the batching process begins. This step combines all the materials, ensuring a homogenous mixture ready for manufacturing.
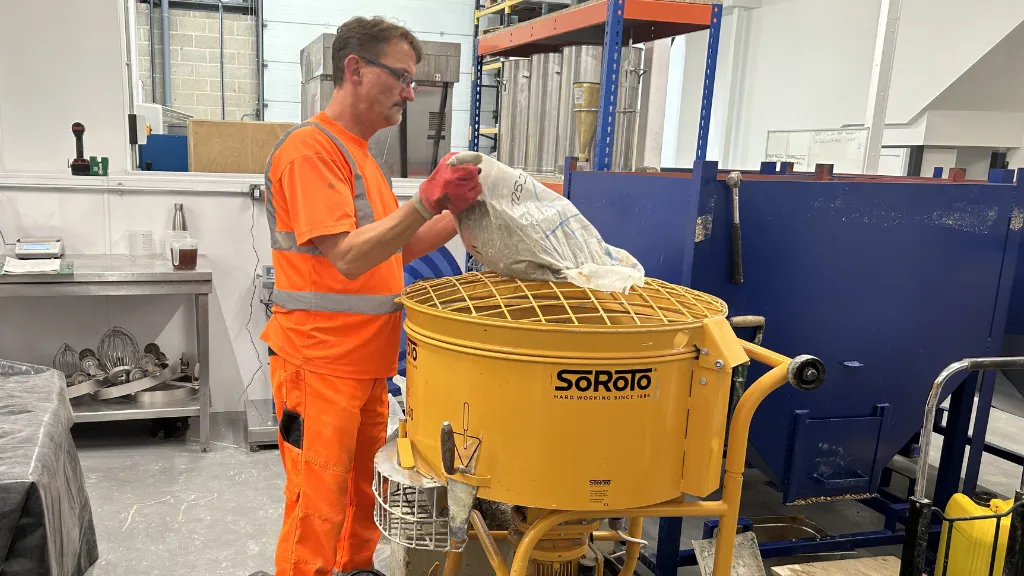
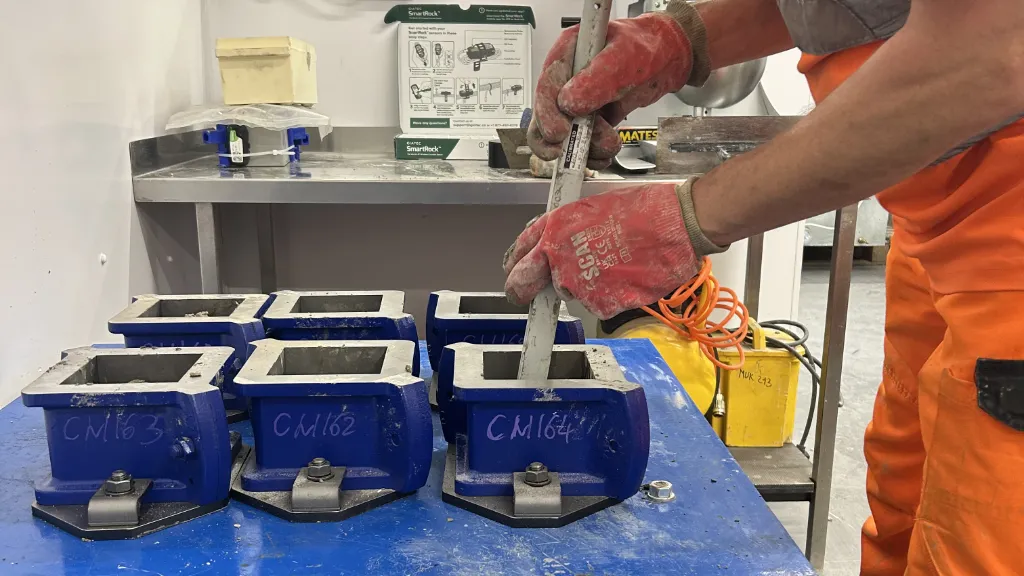
Step 4: Fresh and Hardened Properties
To test the quality and performance of the mix, we subject it to consistence and retention to understand the likelihood of segregation and bleed. We then manufacture concrete cubes for compression testing. These samples are prepared under controlled conditions and provide vital data on compressive strength and durability.
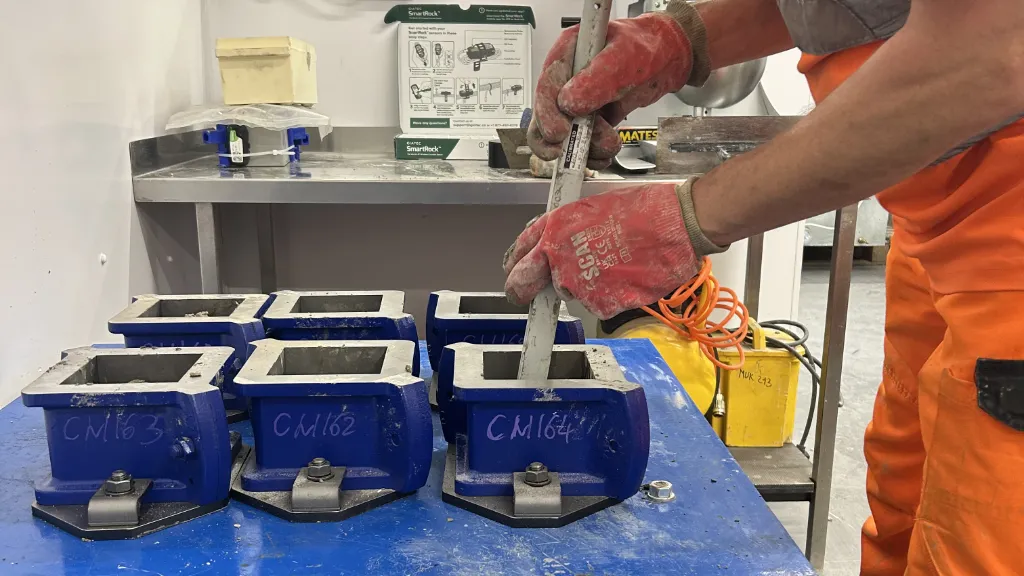
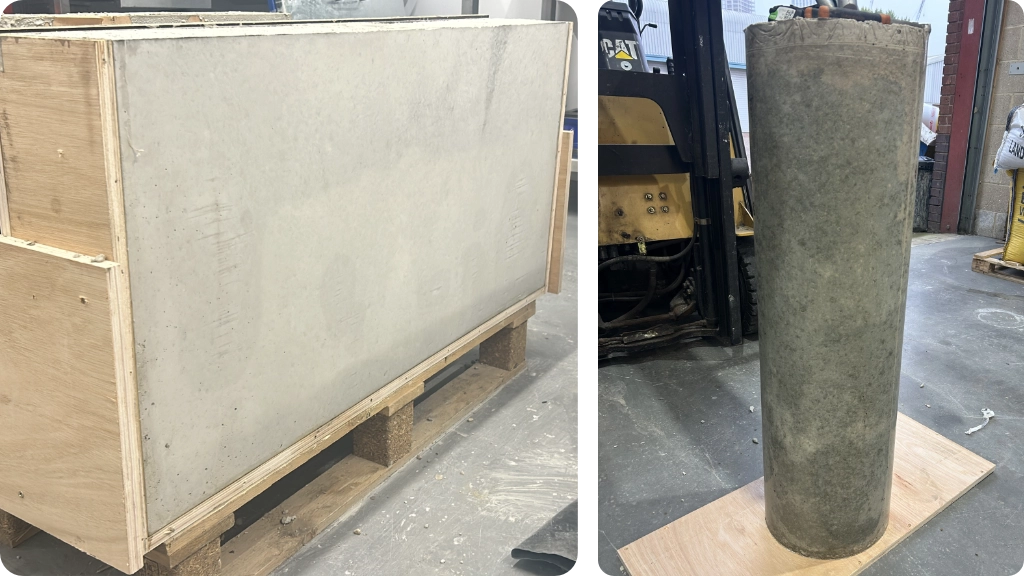
Step 5: Model
In addition to cube testing, we create mockups of larger structures such as walls and columns. This step allows us to simulate real-world applications, assessing the behavior of the concrete in situ and ensuring it meets all necessary specifications.
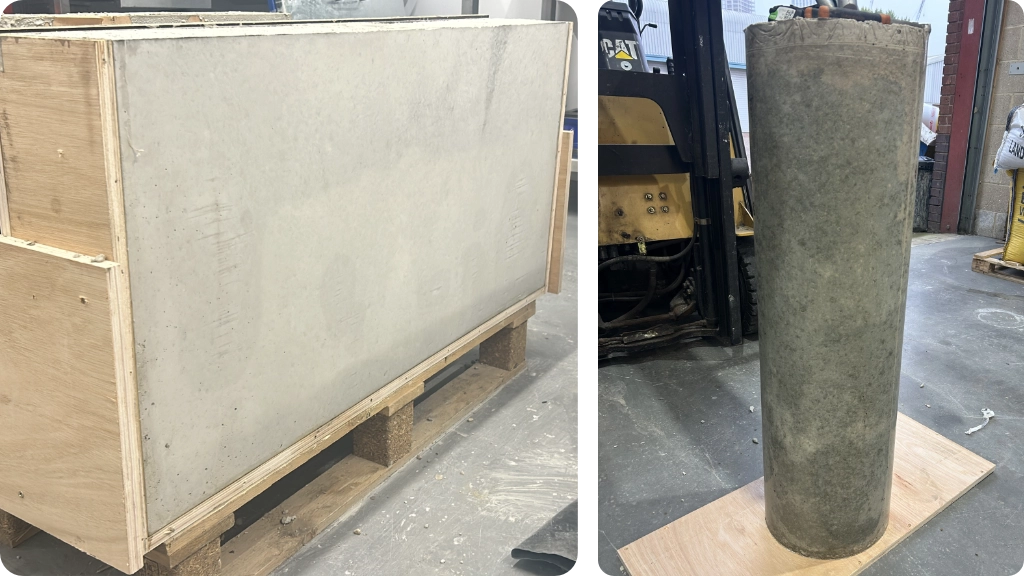
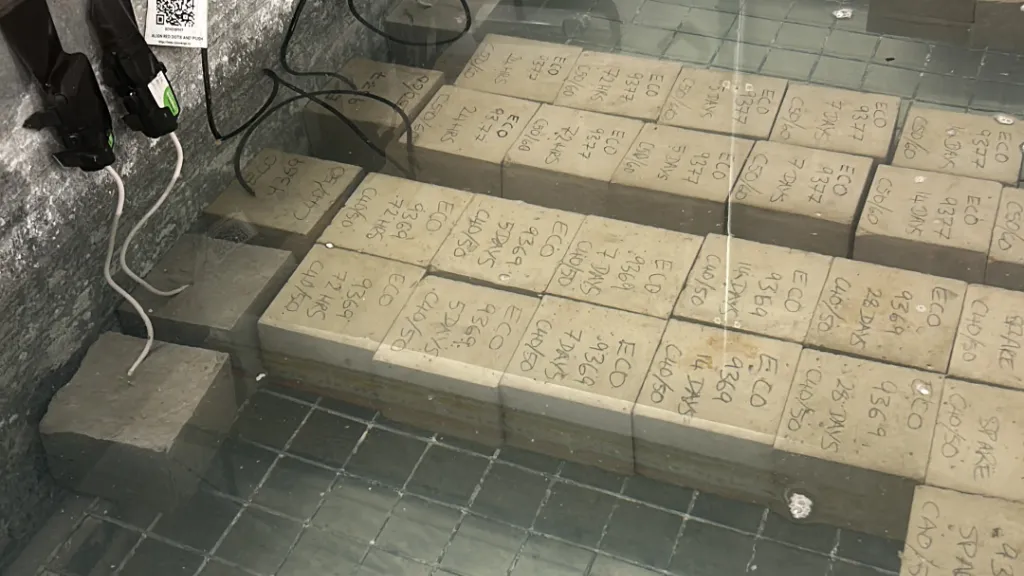
Step 6: Curing
Proper curing is essential for concrete to reach its full strength potential. Our curing process adheres to stringent standards, controlling the environment to ensure optimal strength development of the concrete cubes.
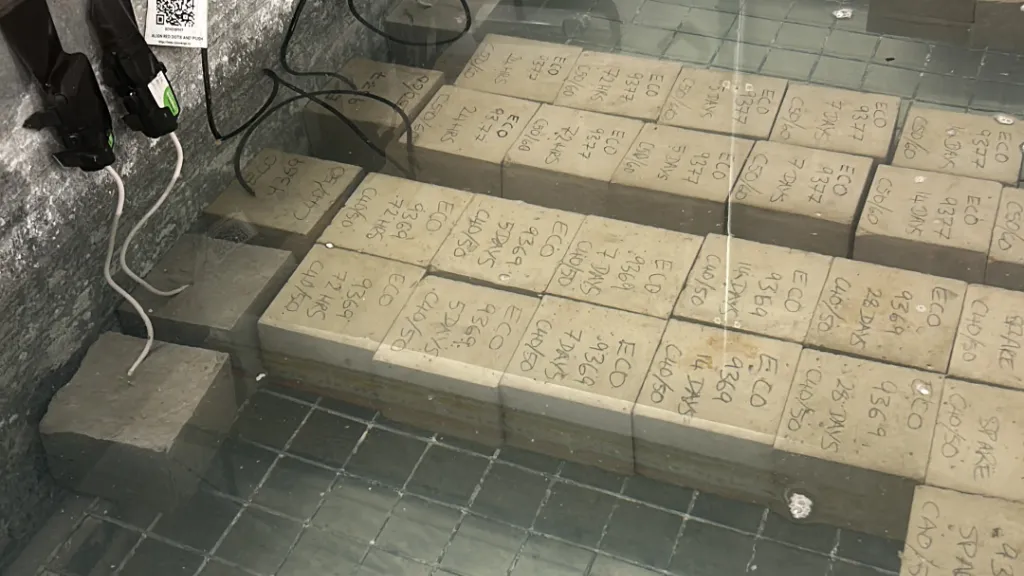
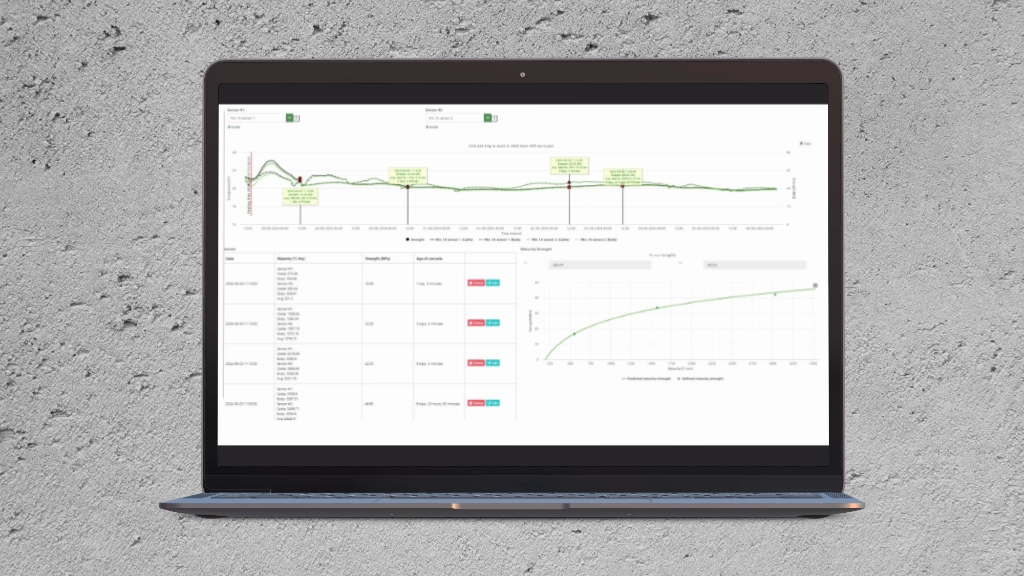
Step 7: Calibration & Maturity
Using advanced calibration and maturity testing techniques, we monitor the progress of concrete strength over time. This data helps predict performance, ensuring the material is ready for application at the right time.
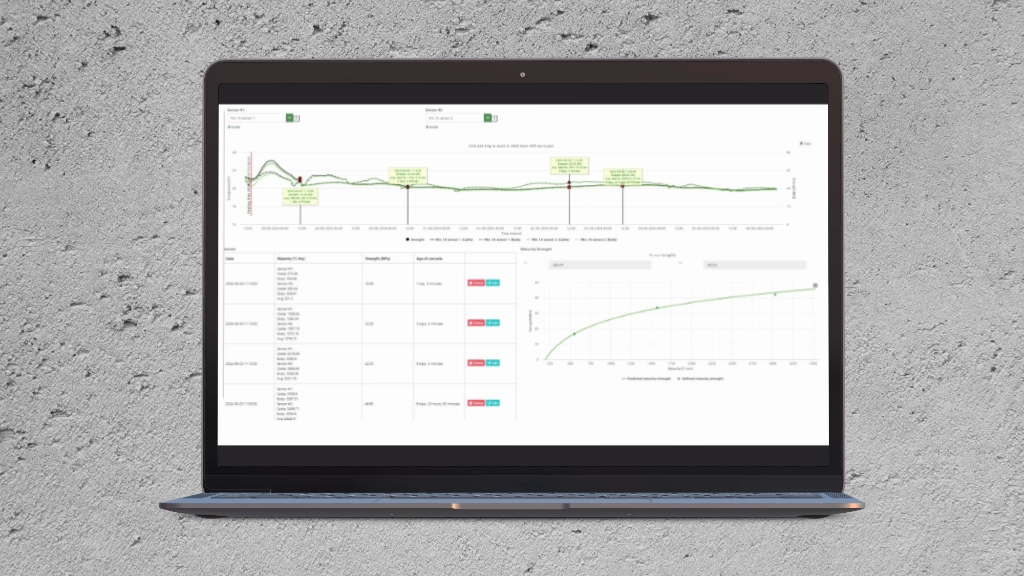
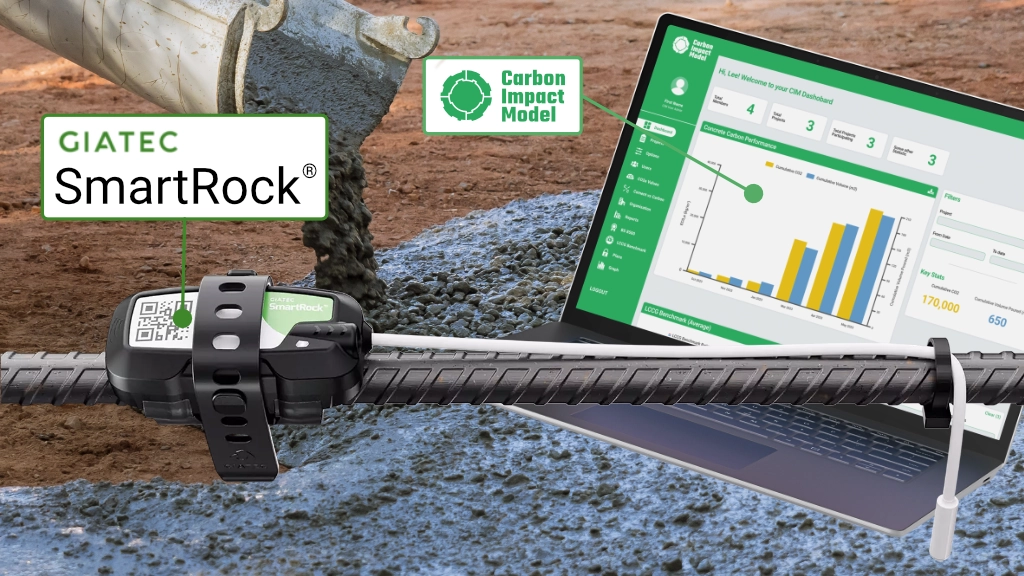
Step 8: Digital Management
All stages of the R&D process are tracked and managed digitally. Our digital systems ensure precision, traceability, and seamless reporting, providing clients with transparent and detailed results at every step, including Carbon Impact Modelling.
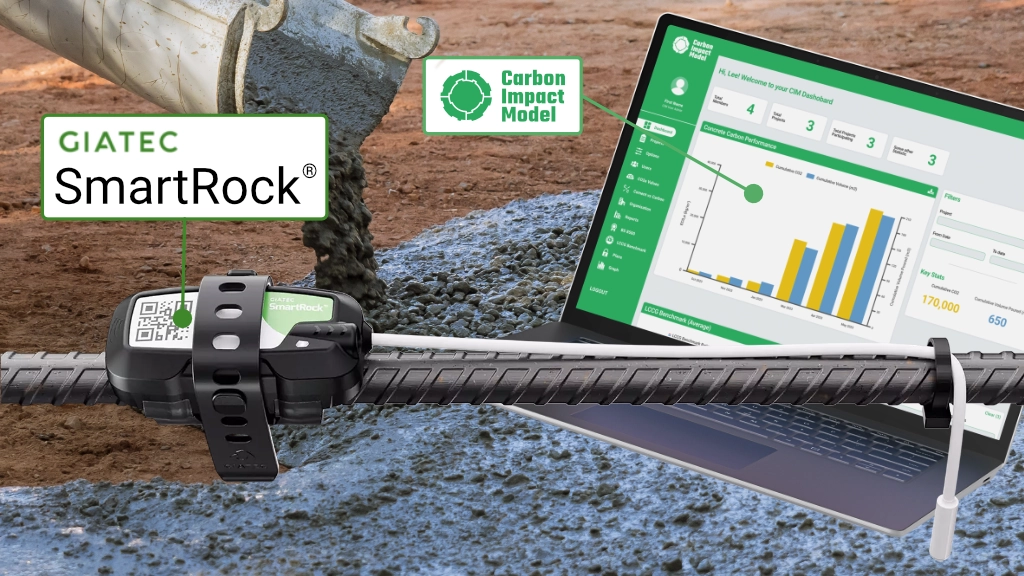
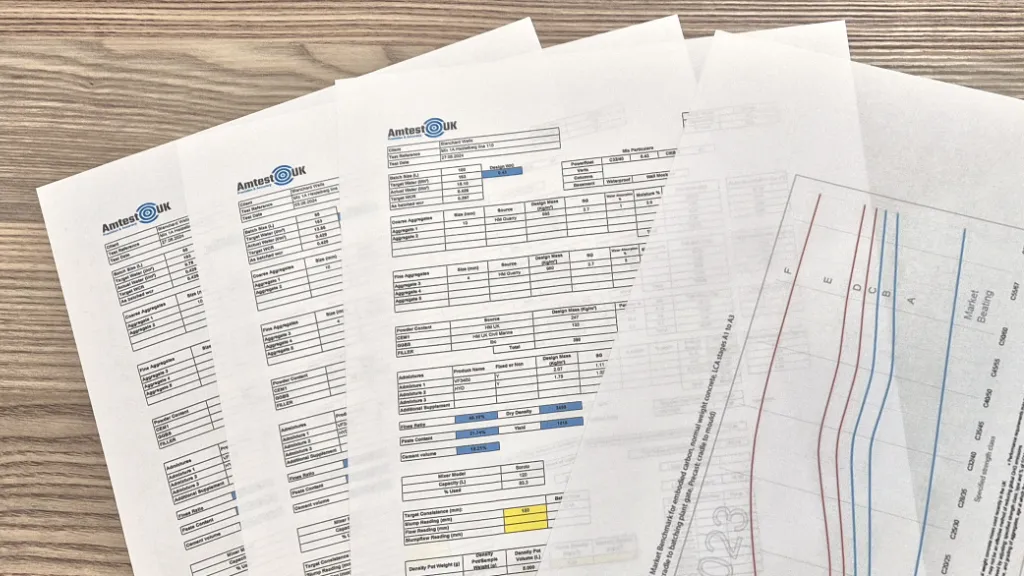
Step 1: Design
The process begins with creating a custom concrete mix design. We analyse the project requirements and design a mix that balances strength, durability, and workability. This step ensures that the final product meets performance criteria for any application.
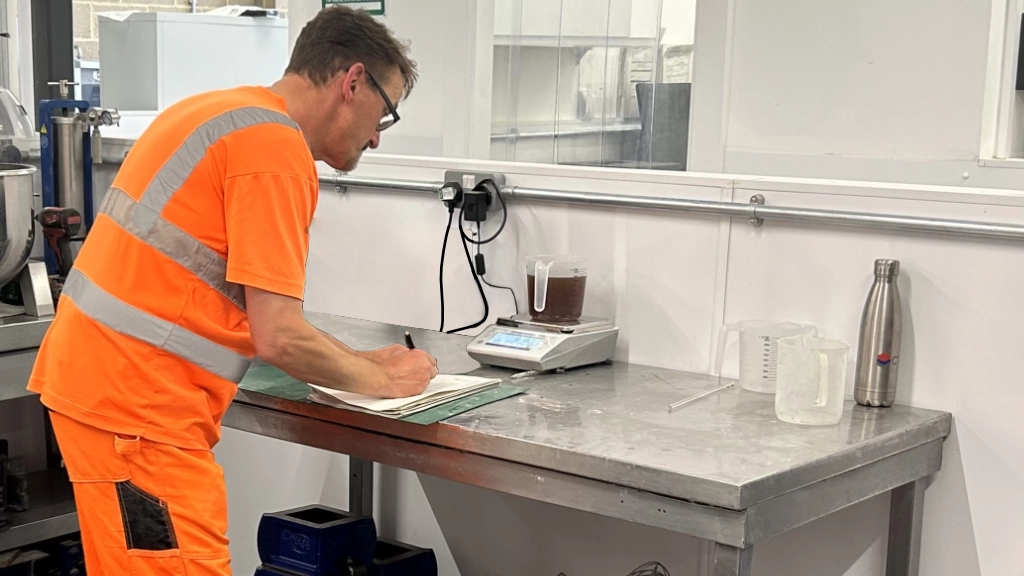
Step 2: Weighing
Accurate measurement of materials is critical. We carefully weigh all components, including cement, aggregates, water, and additives, to maintain consistency and control over the mix’s properties.
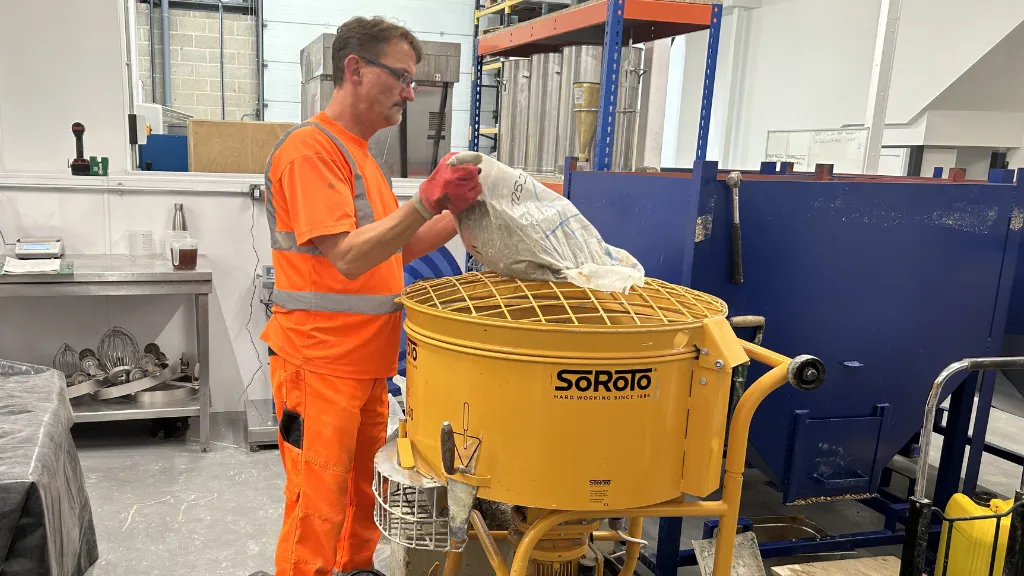
Step 3: Batching
Once the components are weighed, the batching process begins. This step combines all the materials, ensuring a homogenous mixture ready for manufacturing.
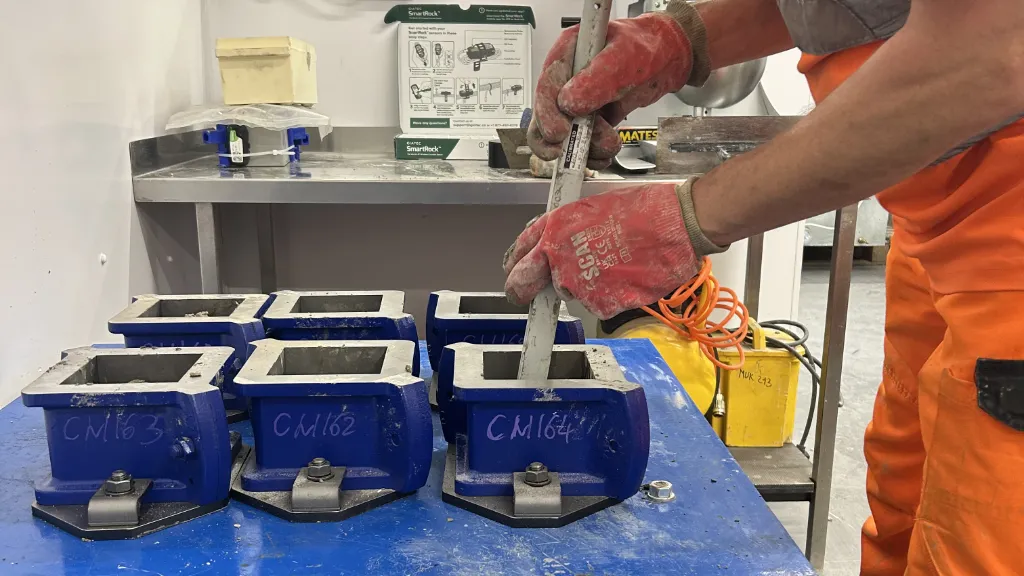
Step 4: Fresh and Hardened Properties
To test the quality and performance of the mix, we subject it to consistence and retention to understand the likelihood of segregation and bleed. We then manufacture concrete cubes for compression testing. These samples are prepared under controlled conditions and provide vital data on compressive strength and durability.
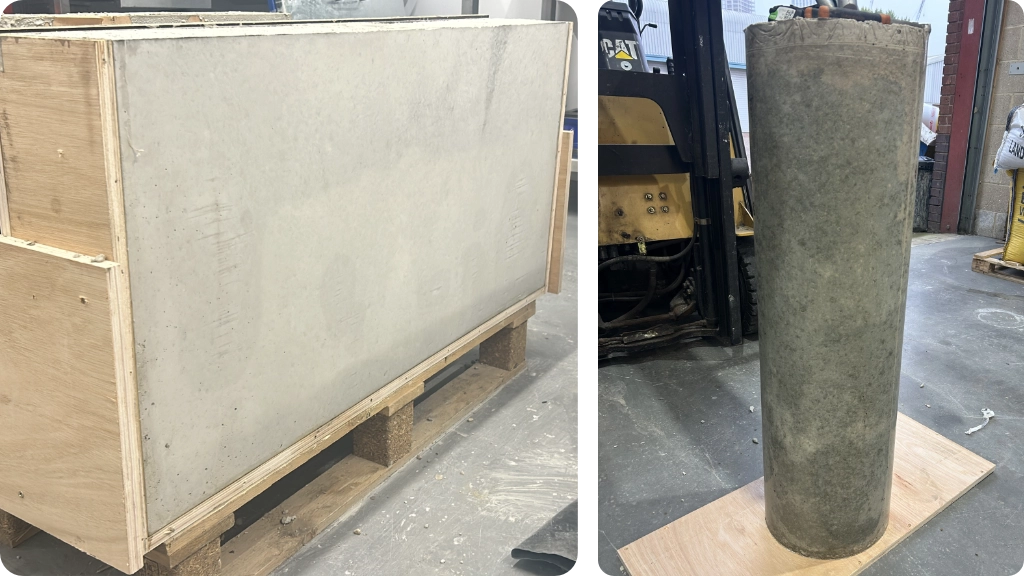
Step 5: Model
In addition to cube testing, we create mockups of larger structures such as walls and columns. This step allows us to simulate real-world applications, assessing the behavior of the concrete in situ and ensuring it meets all necessary specifications.
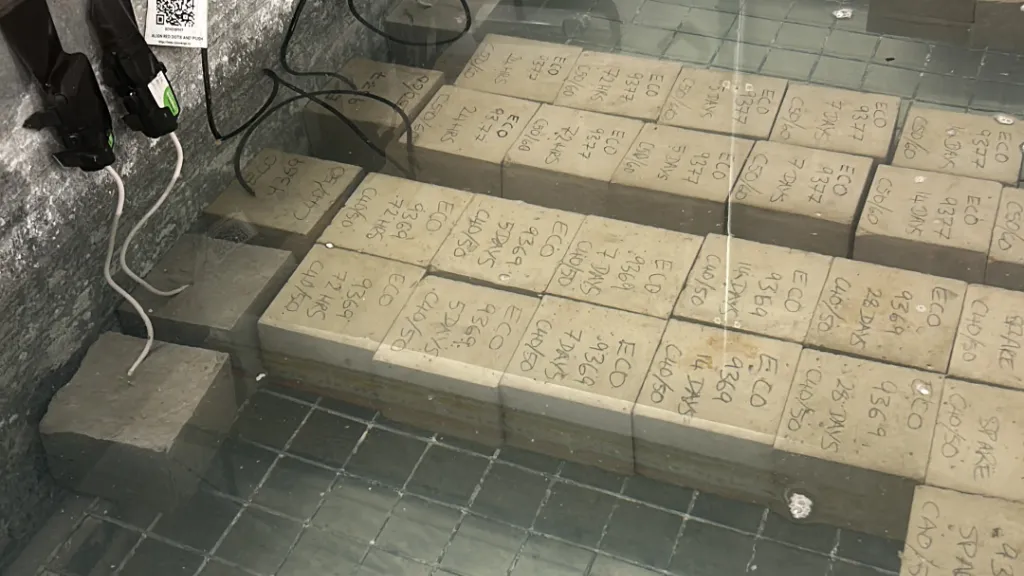
Step 6: Curing
Proper curing is essential for concrete to reach its full strength potential. Our curing process adheres to stringent standards, controlling the environment to ensure optimal strength development of the concrete cubes.
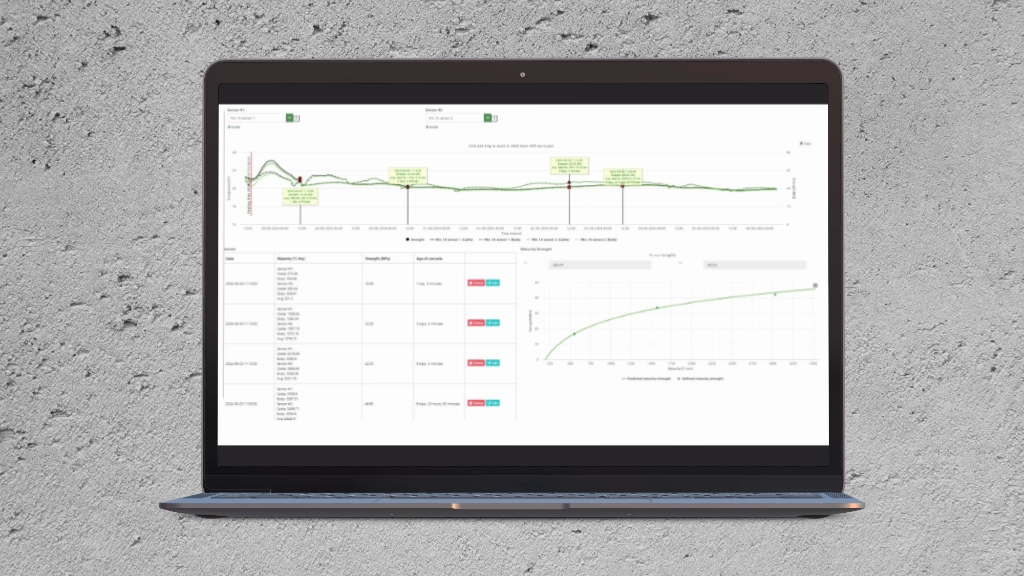
Step 7: Calibration & Maturity
Using advanced calibration and maturity testing techniques, we monitor the progress of concrete strength over time. This data helps predict performance, ensuring the material is ready for application at the right time.
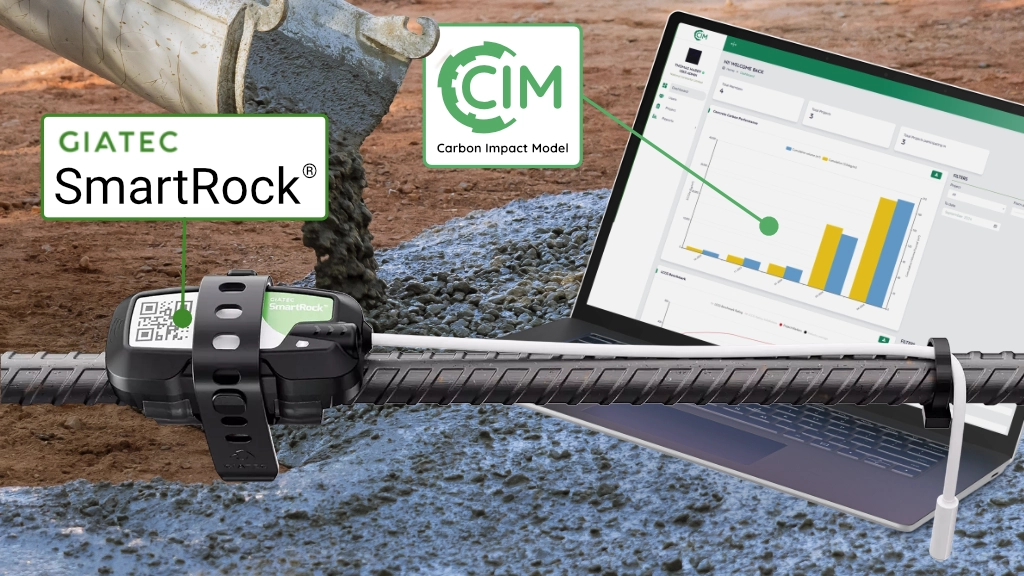
Step 8: Digital Management
All stages of the R&D process are tracked and managed digitally. Our digital systems ensure precision, traceability, and seamless reporting, providing clients with transparent and detailed results at every step, including Carbon Impact Modelling.
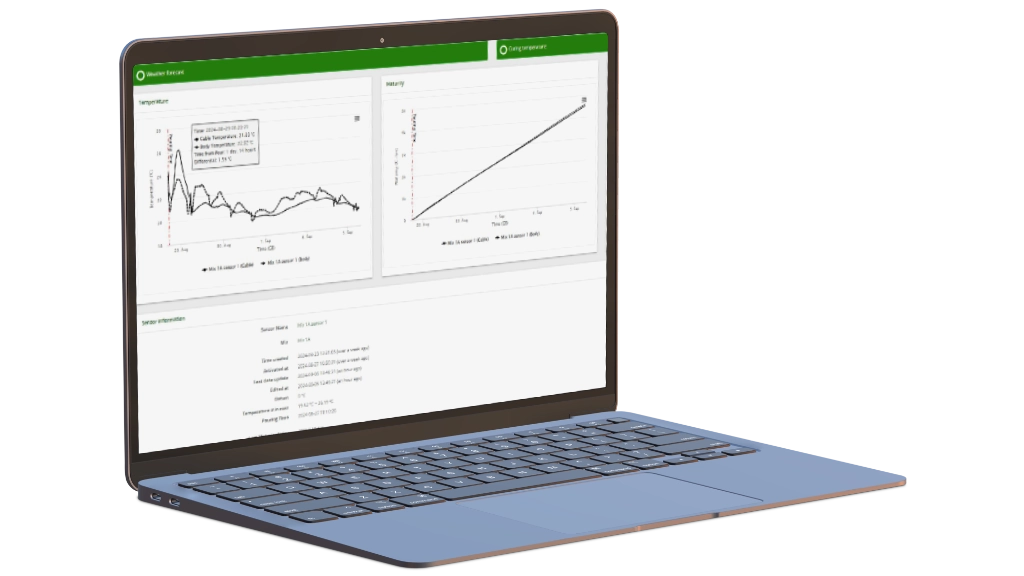
Let's chat!
Our research and development capabilities are open to everyone and provide a unique way to ensure you get the right materials for any project.